
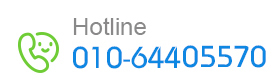
One of the remarkable features of composite materials is the designability of their properties, that is, through the selection of the matrix component system to the structural design of the reinforced materials, the purpose of designing the properties of composite materials is achieved. The direction and quantity of fiber materials can be adjusted according to the force conditions to maximize the bearing capacity of the structure. For example, in the fiber winding process, the winding angle is designed to be 54 ° 44 ′ ′, so that the axial and cyclic strength can be achieved. The composite material so designed is designed because it is designed according to a mechanical model, so the mechanical properties of the composite have anisotropic characteristics(the mechanical properties of the metal material are isotropic), and if the composite material is subjected to secondary mechanical processing, For example, drilling, slotting, etc., the obtained processing surface quality is not satisfactory. The main performance is that the cutting direction of the blade and the direction of fiber arrangement have a direct impact on the acquisition of surface quality. If the obtained processing surface is not functional surface, Can meet the requirements; If the surface obtained by processing, such as the surface obtained by drilling, is used as a close cover, under high pressure(such as at the 1000psi pressure level), the surface quality of the closed cover does not meet the functional requirements. How can we maintain the high mechanical properties of the composites and obtain high quality sealing surfaces? The structure principle of FRP / plastic composite pipe provides a good reference for us. The FRP / plastic composite pipe is an inner lining function layer using the high sealing, toughness, and high-quality surface state of the plastic as the composite pipe, and the structure bearing layer of the composite pipe is made of the high specific strength, high specific modulus, and performance of the FRP material.. The resulting FRP / plastic composite tube has a high quality surface and high sealing properties. This part of the function is borne by the plastic inner lining. The required strength and stiffness part of the function is borne by the FRP structure bearing layer. The performance of the two materials is complementary. Short, Generate synergy effect, bring each other's performance advantage into full play. The tensile strength of the plastic inner lining is generally 20-55 MPa, which is much lower than the FRP tensile strength of 150-350 MPa. At the time of design, all the stress is borne by the FRP structural layer. The strength of the plastic inner lining is ignored. The inner load of the pipeline is transferred from the plastic inner lining to the FRP structure layer. The toughness of the plastic is good, and it can also play a certain damping role.
Our company produces the side pressure film shell side water mouth close cover in the design has borrowed from the FRP / plastic composite pipe design principle. The secret cover of the side opening is designed according to the structural principle of the composite pipe, and the internal pressure is transmitted from the inner lining to the structure layer. In theory, the strength of the inner lining is not unstable on the premise that the inner lining is not unstable(due to the thin inner lining, only about 2mm wall thickness, there is no problem of instability), as long as the elastic modulus of the inner lining is greater than the elastic modulus of the rubber seal ring, That is, it can meet functional requirements. In fact, the elastic modulus of rubber is usually 0.0078 GPa, the elastic modulus of plastics is usually 2GPa, and the elastic modulus of plastics is much larger than the elastic modulus of rubber, so the reliability of the structure is not a problem. By introducing the plastic inner lining into the surface cover of the side water mouth of the lateral pressure film shell, the problem of affecting the sealing performance of the product due to the poor surface quality of the FRP machine is effectively solved.